Abstract:
This white paper aims to provide a general overview of the calibration process for HART (Highway Addressable Remote Transducer) capable electronic valve positioners. As industrial processes become more sophisticated and demand greater precision, electronic valve positioners play a crucial role in ensuring optimal control and efficiency. HART communication protocol enhances the capabilities of these devices by allowing for remote monitoring and configuration. This paper delves into the fundamentals of HART technology, the significance of calibrating electronic valve positioners, and a step- by-step guide to the calibration process.
Introduction:
Electronic valve positioners are integral components in process control systems, enabling precise control of valve positions for fluid and gas flow regulation. With the
integration of HART technology, these devices become even more powerful by providing two-way communication capabilities. Calibrating HART-capable electronic valve
positioners is essential to maintain accuracy, reliability, and overall system efficiency.
Understanding HART Technology:
HART is a digital communication protocol widely used in the process industry. It operates on a 4-20 mA analog signal with a superimposed digital signal, allowing for imultaneous transmission of analog process variables and digital information. HART facilitates bidirectional communication, enabling configuration, monitoring, and diagnostics of field devices, including electronic valve positioners. This white paper aims to provide a general overview of the calibration process for HART (Highway Addressable Remote Transducer) capable electronic valve positioners. As industrial processes become more sophisticated and demand greater precision, electronic valve positioners play a crucial role in ensuring optimal control and efficiency. HART communication protocol enhances the capabilities of these devices by allowing for remote monitoring and configuration. This paper delves into the fundamentals of HART technology, the significance of calibrating electronic valve positioners, and a step-by-step guide to the calibration process.
Introduction:
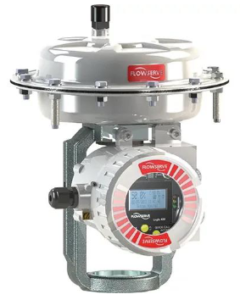
Electronic valve positioners are integral components in process control systems, enabling precise control of valve positions for fluid and gas flow regulation. With the
integration of HART technology, these devices become even more powerful by providing two-way communication capabilities. Calibrating HART-capable electronic valve
positioners is essential to maintain accuracy, reliability, and overall system efficiency.
Understanding HART Technology:
HART is a digital communication protocol widely used in the process industry. It operates on a 4-20 mA analog signal with a superimposed digital signal, allowing for simultaneous transmission of analog process variables and digital information. HART facilitates bidirectional communication, enabling configuration, monitoring, and diagnostics of field devices, including electronic valve positioners.
Significance of Calibrating Electronic Valve Positioners:
Calibration is the process of ensuring that a device’s output corresponds accurately to the input itmreceives. In the context of electronic valve positioners, calibration is crucial for maintaining precision in controlling valve positions. Proper calibration ensures that the valve responds accurately to control signals, contributing to the efficiency and safety of industrial processes.
A quick note before we start:
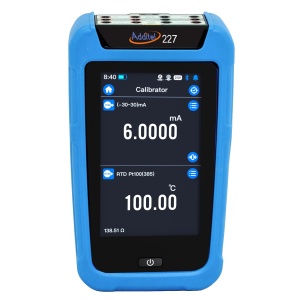
Some HART capable valve positioners have a “protection” or “adjustment” mode, which means that parameters can only be changed after entering this mode. It is important to note that while in this type of mode, the moving parts of the valve will not articulate with the change of commands. It may be necessary to switch the modes of the device under test between changing parameters and the testing/calibration process.
Calibration Process for HART-Capable Electronic Valve Positioners:
1. Preparation
- Ensure the valve positioner is properly installed and all connections are secure.
- Refer to the manufacturer’s manual if necessary.
- Verify the power supply and communication connections.
- Check for any physical damage or obstructions in the valve assembly.
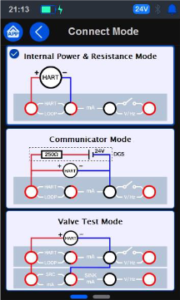
2. Initialization:
- Power on the electronic valve positioner.
- Establish communication with the HART device using a HART communicator.
- The Additel 227 with HART communications includes a graphical wiring feature that helps with configuring the communication (see figure 1)
- Verify the device identification and capabilities.
- HART commands are established in (3) categories, universal, common practice and device specific. It is generally best to use your communicator of choice to send a “universal” command, such as “read manufacture and device type” to ensure that communications are working properly.
3. Baseline Calibration:
- Set the valve positioner to a reference point.
- Send a calibration command through the HART communicator.
- Record the actual valve position and compare it with the reference point.
Figure 2: ADT227 Communicating via HART with a Field Vue valve positioner.
4. Gain and Zero Adjustment:
- Adjust the gain to match the expected output for a given input signal.
- Zero the valve positioner to eliminate any offset in the output.
5. Performance Testing:
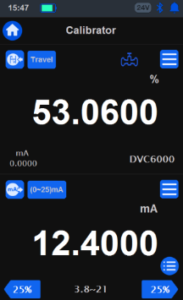
- Execute a series of input signals to assess the valve positioner’s response.
- Verify that the valve responds accurately and consistently to control signals.
6. Fine-Tuning:
- Make minor adjustments as needed to optimize performance.
- Record the final calibration settings.
7. Challenges and Troubleshooting:
- Identify common challenges in the calibration process.
- Provide troubleshooting tips for addressing calibration issues.
8. Future Trends and Considerations:
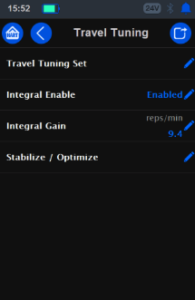
Figure 3: ADT227 Testing of DVC 6000 Transmitter
- Explore emerging technologies in electronic valve positioners.
- Discuss potential advancements in HART communication protocol.
Conclusion:
Calibrating HART-capable electronic valve positioners is a critical aspect of maintaining precision and reliability in industrial processes. This white paper has provided a general guide to the calibration process, emphasizing the importance of each step. As technology continues to evolve, staying informed about the latest trends and advancements in electronic valve positioners and communication protocols is essential for optimizing process control systems.